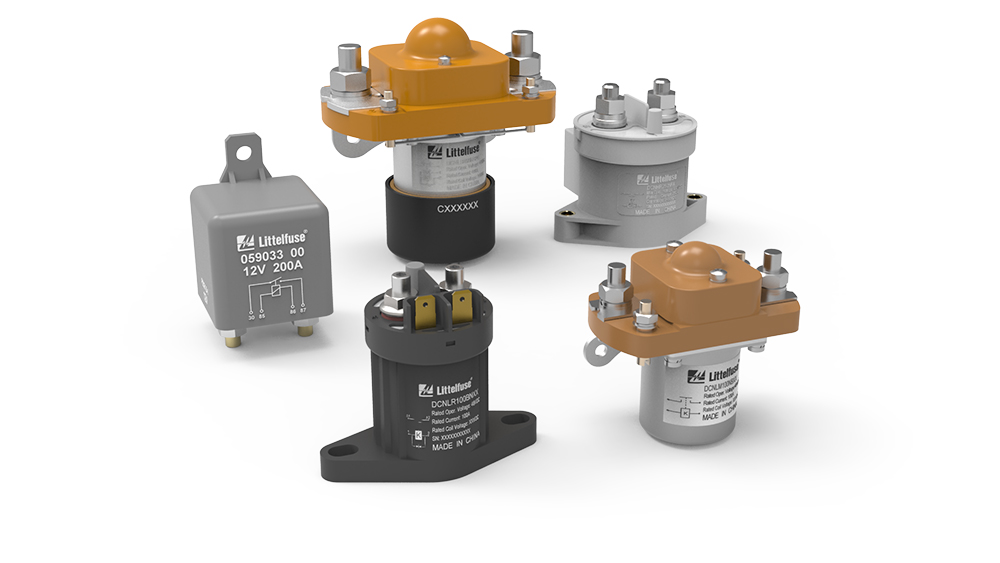
Sponsored by TTI.
Polarization in DC Contactors for high-voltage electric vehicle applications.
Littelfuse offers both polarized and non-polarized high-voltage (HV) DC contactors or relays to meet a wide range of electric vehicle (EV) application requirements. Appropriate for the majority of HV EV applications, DC contactors with polarization offer a significant advantage in terms of electric cycle life. HV relays are designed with magnetic blowouts and gas-filled contact chambers, which allow them to make/break at higher voltages. This application note discusses these design elements and the functionality of polarization in HV DC contactors.
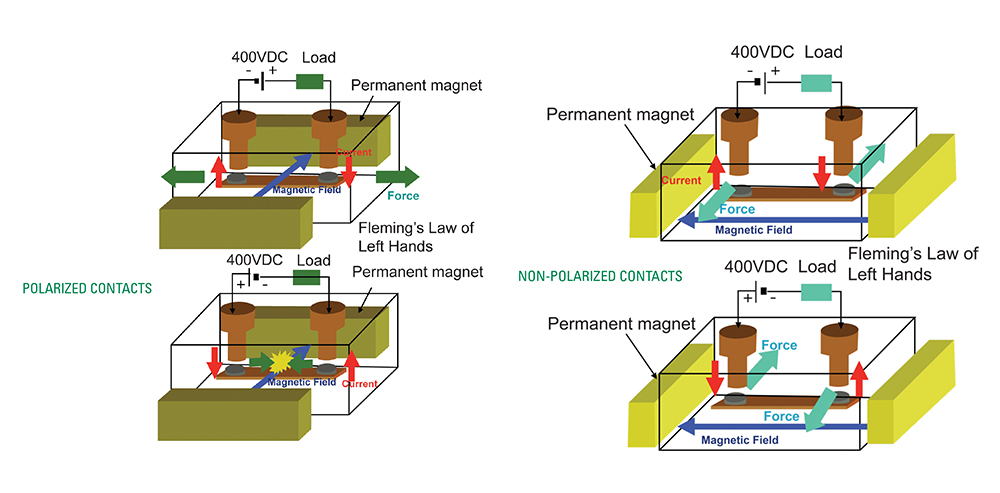
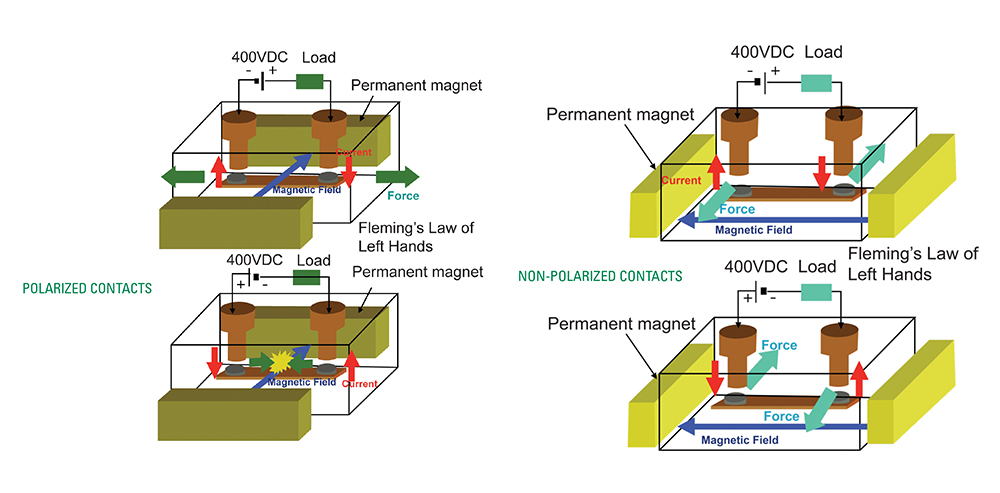
Polarized HV Contactors vs. Non-Polarized HV Contactors
Both polarized and non-polarized contactors allow current to flow in either direction. Polarization, however, greatly improves the make/break capability and cycle life in HV relays.
Polarized relays have magnetic blowouts that optimize the arc quenching when the current is flowing from the positive (+) input to a negative (-) output. This leads to the best quenching of the arc and the longest electric cycle life of the relay. If the relay opens on a circuit with the current reversed, it has significantly reduced cycle life. For this reason, contacts are marked as positive (+) and negative (-) on polarized relays, and proper installation to ensure the correct current flow is imperative.
Non-polarized relays have magnetic fields that are balanced to quench the arc with current running in either direction. The magnets cannot be placed as effectively, which causes greater arcing, and therefore, greater wear and shorter cycle life. The greater arcing in non-polarized contactors leads to about a 50% reduction in electrical cycle life from polarized values.
How Magnetic Blowouts and Gas-Filled Chambers Improve the Cycle Life of an HV DC Contactor
When an AC relay opens, the arc will extinguish quickly, as the voltage naturally passes through the 0V point multiple times per second. For DC relays, on the other hand, the only thing that quenches the arc is resistance as set by the distance from the input to the output through the media in the contact chamber.
Effectively extinguishing the electrical arc requires:
- Media Resistance – Inert gas inside the contact chamber provides a higher ionization energy media. For an arc to propagate and move through this gas, it needs to expend more energy than it would if it were moving through air.
- Distance – To lengthen the distance an arc must travel, we use a combination of double-opening contacts and magnetic blowouts.
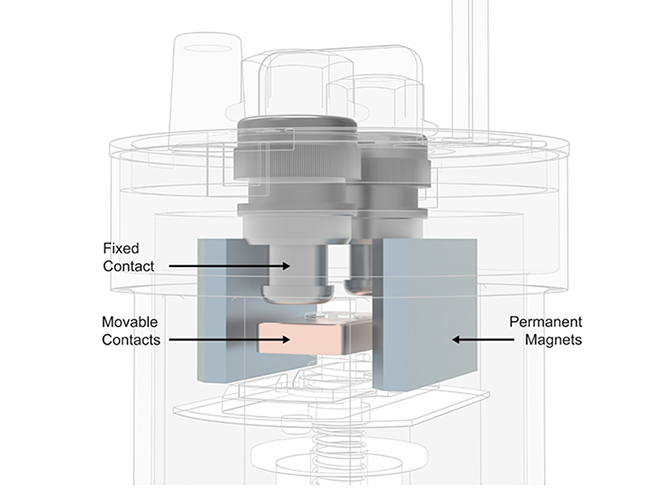
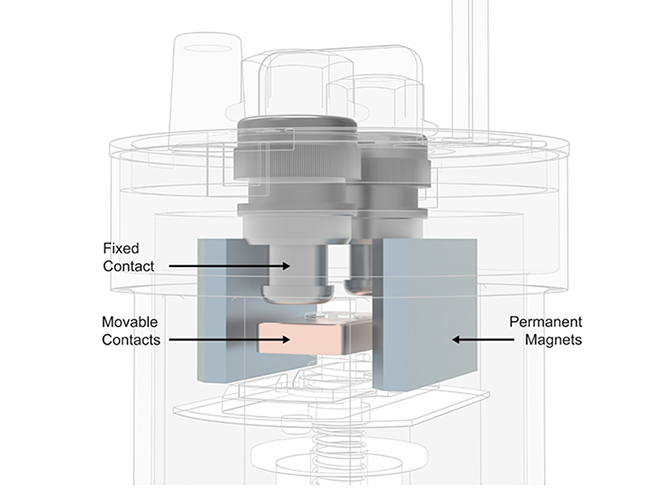
Double-opening contacts effectively double the opening distance based on the same motion of the moving contact bridge.




Magnetic blowouts effectively lengthen the opening distance by forcing the path of the arc to the outer edge of the contact chamber along magnetic field lines created by permanent magnets in the contact area. The magnetic field lines interact with the arc by charge, so the arrangement of the magnets determines how effective the magnets are in extending the path of the arc.
Polarized magnets with the correct direction of current flow get the most displacement of the arc and the highest amount of quenching, as they have the best alignment of the field lines and the arc. When the current direction is reversed the magnetic field lines do not line up well, and the arc displacement is significantly reduced leading to longer arc duration and more damage to the contacts.
Non-polarized magnets are a compromise. when the current direction is correct to the polarization, the magnetic fields don’t line up as well compared to polarized magnets, but they line up better than polarized magnets when the current is reversed. While the electrical cycle life is reduced by about 50% from the polarized relay in the optimum situation, it is much better in the situation where the opening takes place with the current reversed.
Choosing Polarized vs. Non-Polarized HV DC Contactors
As noted, polarized and non-polarized contactors allow current to flow in both directions. Choosing a polarized HV relay or a non-polarized relay comes down to understanding the make/break and electrical cycle life considerations of an application.
The electrical cycle life is usually defined at a set voltage and rated current. In the life of a vehicle, though, most contactor cycles are low or zero current. Therefore, full voltage and current cycles are rare, and a relatively lower number of full voltage and current cycles is very common for HV contactors.
Even in applications that require short durations of current flowing back through the contactor, as is the case with regenerative braking, the current flows in the primary direction most of the time. Since a switch event during regenerative braking would be very rare, the risk to the system would be very low.
While non-polarized HV contactors may be appropriate in a few cases where current flows frequently in the reverse direction, a polarized DC contactor is more often the best choice for HV EV applications of greater than 350V.