Electric vehicles (EVs) can use various types of electric motors, each with its own characteristics, advantages, and disadvantages. The primary types of electric motors used in EVs are:
- Brushed DC Motors:
- Operation: In a brushed DC motor, electricity flows through brushes and a commutator, which cause the rotor (armature) to rotate.
- Advantages: Simple design, cost-effective, and easy to control.
- Disadvantages: Limited efficiency, maintenance requirements due to brushes wear.
- Brushless DC Motors (BLDC):
- Operation: Similar to brushed DC motors, but without brushes. Instead, they have electronic controllers to switch the current direction.
- Advantages: More efficient and longer lifespan compared to brushed motors, less maintenance, and higher power density.
- Disadvantages: Generally more expensive than brushed DC motors.
- Induction Motors (AC Motors):
- Operation: Induction motors use alternating current (AC) to induce a magnetic field in the rotor, causing it to turn.
- Advantages: Robust design, high efficiency, and no brushes to wear out.
- Disadvantages: More complex control systems, slightly lower power density compared to some DC motors.
- Permanent Magnet Synchronous Motors (PMSM):
- Operation: Similar to BLDC motors, but with permanent magnets in the rotor instead of electromagnets.
- Advantages: High efficiency, good power density, and precise control.
- Disadvantages: More expensive to manufacture than some other motor types.
- Switched Reluctance Motors (SRM):
- Operation: SRMs use magnetic reluctance to generate motion. The rotor moves to align with the magnetic field.
- Advantages: Robust, simple design, potentially lower manufacturing cost.
- Disadvantages: Historically, control systems for SRMs have been more complex.
understanding difference in various electric motors for evs
here is a detailed discussion on difference between various types of electric motors used in electric vehicles.
1. Brushed DC Motors
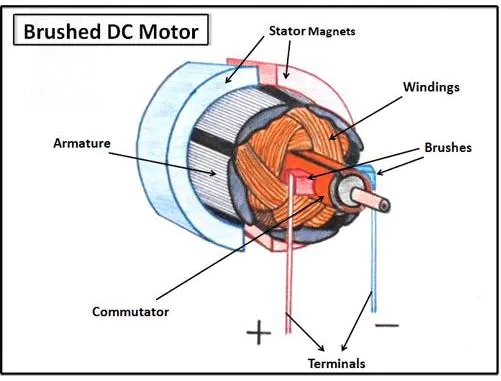
Brushed DC motors are a type of electric motor that operates using direct current (DC). They are one of the simplest and oldest types of electric motors, characterized by the use of brushes and a commutator for the flow of electric current. Here are the key details about brushed DC motors:
Components and Operation:
- Rotor (Armature): The rotor is the rotating part of the motor and is usually made of a coil of wire wound around an iron core.
- Stator: The stator is the stationary part of the motor and typically contains magnets or coils that produce a magnetic field.
- Brushes: Brushes are typically made of carbon and are in direct contact with the commutator. They carry electrical current to the armature.
- Commutator: The commutator is a rotary switch mounted on the rotor. It reverses the direction of the electric current in the rotor windings, ensuring continuous rotation.
Operation Steps:
- Current Flow: DC power is supplied to the motor, causing current to flow through the brushes to the commutator.
- Magnetic Field: As current passes through the armature, a magnetic field is generated. The interaction between this magnetic field and the magnetic field produced by the stator causes the rotor to turn.
- Commutator Action: The commutator ensures that the direction of the current in the rotor windings changes at the appropriate times, ensuring continuous rotation.
- Brush Wear: Over time, the brushes experience wear due to friction with the commutator. Regular maintenance may involve replacing brushes.
Advantages:
- Simple Design: Brushed DC motors have a relatively simple and straightforward design.
- Cost-Effective: They are generally less expensive to manufacture compared to more complex motor types.
- Easy to Control: Controlling the speed of a brushed DC motor is relatively simple.
Disadvantages:
- Limited Efficiency: Brushed DC motors are not as efficient as some other motor types, especially at higher speeds.
- Maintenance Requirements: The brushes in contact with the commutator wear out over time, requiring periodic maintenance.
- Electromagnetic Interference (EMI): The operation of brushed DC motors can generate electromagnetic interference.
While brushed DC motors are still used in certain applications, especially where cost and simplicity are crucial, many modern electric vehicles and appliances use more advanced motor technologies like brushless DC motors, induction motors, or permanent magnet synchronous motors. These alternatives offer improved efficiency and reduced maintenance requirements.
2. Brushless DC Motors (BLDC)
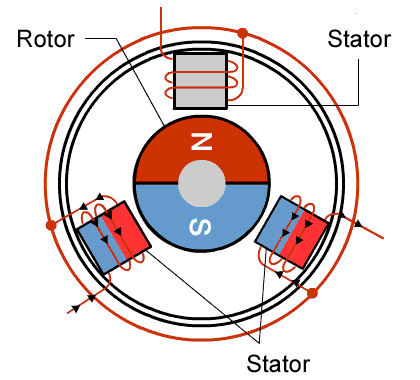
Brushless DC (BLDC) motors are a type of electric motor that operates using direct current (DC) and is distinguished by the absence of brushes and a commutator. Instead, BLDC motors use electronic commutation systems to control the current flow. Here are the key details about brushless DC motors:
Components and Operation:
- Stator: Similar to brushed DC motors, the stator in a BLDC motor is the stationary part and typically contains coils that produce a magnetic field.
- Rotor (Armature): The rotor is the rotating part of the motor, usually equipped with permanent magnets.
- Electronic Controller: BLDC motors require an electronic controller to manage the commutation of the stator windings. The controller precisely controls the timing and sequence of the current flow, eliminating the need for physical brushes and commutators.
Operation Steps:
- Rotor Movement: The permanent magnets on the rotor produce a magnetic field. As the rotor turns, the magnetic field interacts with the stator’s magnetic field.
- Electronic Commutation: The electronic controller determines when to energize the stator coils to create a magnetic field that repels or attracts the permanent magnets on the rotor. This electronic commutation ensures a smooth and continuous rotation of the motor.
- Efficiency: BLDC motors are generally more efficient than brushed DC motors because there are no brushes causing friction and no energy losses due to brush and commutator wear.
Advantages:
- High Efficiency: BLDC motors typically have higher efficiency compared to brushed DC motors.
- Reduced Maintenance: With no brushes to wear out, BLDC motors require less maintenance.
- Better Performance: BLDC motors can provide better performance in terms of speed control, torque, and power density.
- Longer Lifespan: The absence of brushes and commutators contributes to a longer lifespan.
- Reduced Electromagnetic Interference (EMI): BLDC motors generate less electromagnetic interference compared to brushed DC motors.
Disadvantages:
- Complex Control Systems: The control systems for BLDC motors are more complex compared to brushed DC motors, requiring sophisticated electronics.
- Higher Initial Cost: BLDC motors can be more expensive to manufacture than brushed DC motors, primarily due to the electronic control systems.
- Sensorless vs. Sensored: Some BLDC motors are designed to operate sensorlessly, while others use sensors for precise control. Sensorless designs may have limitations in certain applications.
BLDC motors are widely used in various applications, including electric vehicles, HVAC systems, appliances, and industrial machinery. Their efficiency, reliability, and performance make them a popular choice in modern electric systems. Advances in control systems and manufacturing processes continue to improve the capabilities of BLDC motors.
3. Induction Motors (AC Motors)
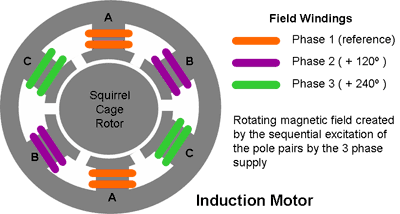
Induction motors, also known as asynchronous motors, are a type of alternating current (AC) electric motor widely used in various applications. They operate on the principle of electromagnetic induction and are known for their reliability and robust design. Here are the key details about induction motors:
Components and Operation:
- Stator: The stator is the stationary part of the motor and consists of a laminated iron core with evenly spaced windings connected to the AC power supply. The stator windings create a rotating magnetic field when energized.
- Rotor: The rotor is the rotating part of the motor. It can be of different types: squirrel cage rotor (most common) or wound rotor. The rotor is placed inside the stator and is allowed to rotate freely.
- Operation Steps:
- When AC power is supplied to the stator windings, it produces a rotating magnetic field.
- The rotating magnetic field induces a voltage in the rotor windings (or bars in the case of a squirrel cage rotor).
- This induced voltage in the rotor produces a current that generates a magnetic field.
- The interaction between the rotating magnetic field in the stator and the induced magnetic field in the rotor causes the rotor to turn, producing mechanical rotation.
- The rotor always lags slightly behind the rotating magnetic field of the stator, resulting in the term “asynchronous” motor.
Advantages:
- Simple Design: Induction motors have a relatively simple and robust design.
- Low Maintenance: They have fewer moving parts compared to some other motor types, leading to lower maintenance requirements.
- Durable: Induction motors are known for their durability and long lifespan.
- Cost-Effective: They are generally cost-effective to manufacture.
- No Brushes: Unlike brushed DC motors, induction motors do not have brushes, reducing wear and maintenance.
Disadvantages:
- Fixed Speed: Induction motors operate at a fixed speed determined by the frequency of the AC power supply. This can be a limitation in applications requiring variable speeds without additional control devices.
- Slip: There is always a slight difference in speed (slip) between the rotating magnetic field and the rotor, leading to a loss of energy.
- Complex Speed Control: Achieving variable speeds with induction motors requires additional control systems, such as variable frequency drives (VFDs).
Applications:
- Induction motors are widely used in industrial applications, such as pumps, fans, compressors, and conveyor systems.
- They are commonly found in household appliances like washing machines, refrigerators, and air conditioners.
- Induction motors are often used in electric vehicles for various components like fans and pumps.
Overall, induction motors are versatile and well-suited for applications where a simple, reliable, and cost-effective motor solution is needed. Advances in control technologies, such as VFDs, have expanded their use in applications requiring variable speed control.
4. Permanent Magnet Synchronous Motors (PMSM)
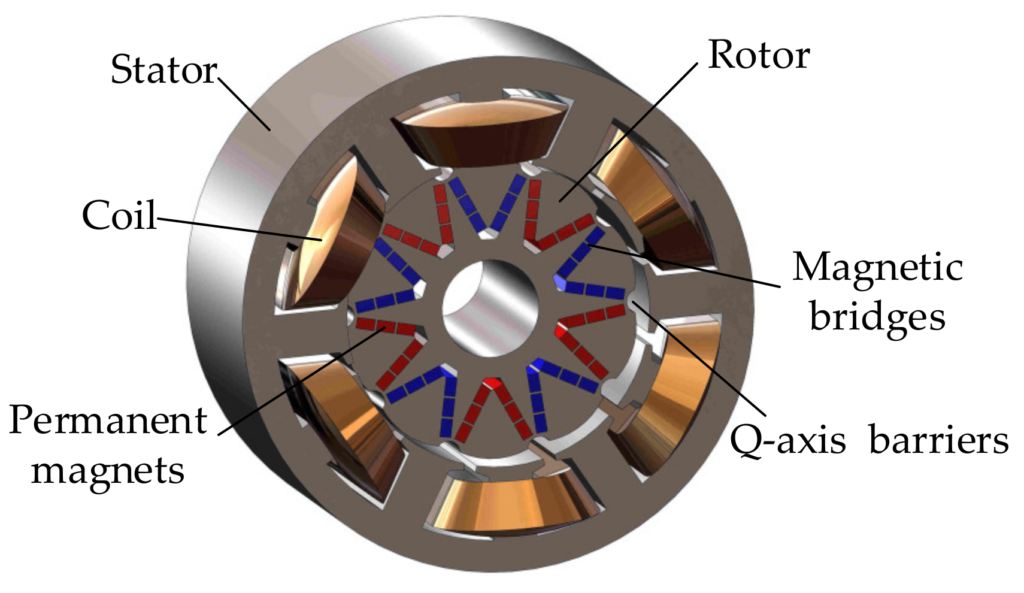
Permanent Magnet Synchronous Motors (PMSM) are a type of electric motor that operates using alternating current (AC). These motors are characterized by the use of permanent magnets in the rotor, eliminating the need for a winding or coil in the rotor. PMSMs offer several advantages and are commonly used in various applications. Here are the key details about Permanent Magnet Synchronous Motors:
Components and Operation:
- Stator: The stator is the stationary part of the motor and contains windings that produce a rotating magnetic field when energized with AC power.
- Rotor: The rotor is the rotating part of the motor and contains permanent magnets. The magnetic field of the rotor interacts with the rotating magnetic field produced by the stator.
- Permanent Magnets: Instead of using coils or windings in the rotor, PMSMs have permanent magnets, typically made of rare-earth materials such as neodymium or samarium-cobalt. These magnets create a strong and constant magnetic field.
Operation Steps:
- AC power is supplied to the stator windings, producing a rotating magnetic field.
- The permanent magnets in the rotor are attracted to or repelled by the rotating magnetic field, causing the rotor to turn.
- The synchronous operation ensures that the rotor rotates at the same frequency as the stator’s rotating magnetic field.
- PMSMs can achieve synchronous speed, meaning there is no slip between the rotating magnetic field and the rotor.
Advantages:
- High Efficiency: PMSMs generally offer high efficiency, especially at full load.
- High Power Density: They provide a high power-to-weight ratio, making them suitable for applications with space constraints.
- Precise Control: PMSMs can be precisely controlled for speed and torque, making them suitable for applications requiring variable speed operation.
- Low Maintenance: The absence of brushes and a commutator reduces maintenance requirements.
- Regenerative Braking: PMSMs can support regenerative braking, converting kinetic energy back into electrical energy during deceleration.
Disadvantages:
- Cost: Permanent magnets, especially rare-earth magnets, can contribute to the overall cost of the motor.
- Complex Control Systems: Achieving precise control may require sophisticated control systems.
Applications:
- PMSMs are commonly used in various applications, including industrial machinery, robotics, HVAC systems, electric vehicles, and more.
- They are favored in applications where high efficiency, precise control, and compact design are crucial.
- PMSMs are often used in electric and hybrid vehicles for propulsion systems.
Overall, Permanent Magnet Synchronous Motors are versatile and well-suited for applications where precise control, high efficiency, and low maintenance are essential. Advances in magnet technology and control systems continue to improve the performance and applicability of PMSMs in various industries.
5. Switched Reluctance Motors (SRM):
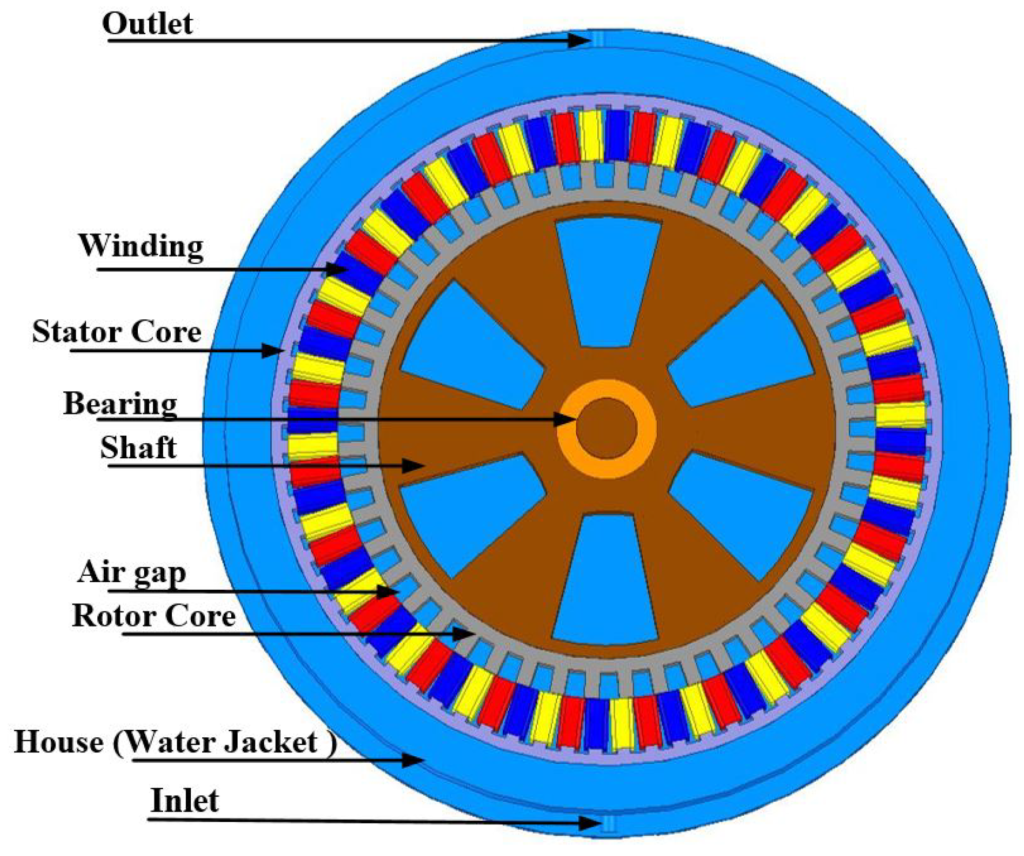
Switched Reluctance Motors (SRM) are a type of electric motor that operates based on the principle of reluctance torque. Unlike many other types of motors that use permanent magnets or wound coils in the rotor, SRMs have a rotor with no windings or magnets. Instead, they rely on the tendency of magnetic materials to move toward regions of higher magnetic flux. Here are the key details about Switched Reluctance Motors:
Components and Operation:
- Stator: The stator is the stationary part of the motor and contains coils that produce a magnetic field when energized.
- Rotor: The rotor is the moving part of the motor and is typically made of laminated steel. It does not have permanent magnets or windings.
- Control System: SRMs require a sophisticated control system to precisely control the timing of current flow through the stator windings.
Operation Steps:
- The stator windings are sequentially energized in a way that creates a magnetic field, causing the rotor to align itself with the stator’s magnetic field due to magnetic reluctance.
- As the rotor aligns itself, the reluctance (resistance to magnetic flux) decreases, and the rotor moves to minimize this reluctance.
- The control system continually adjusts the timing of stator winding energization to maintain the rotor’s optimal position relative to the stator magnetic field.
- SRMs operate based on the principle that the rotor will always seek the position of minimum reluctance, and the control system exploits this to produce motion.
Advantages:
- Robust Design: SRMs have a simple and robust design with fewer mechanical parts, making them suitable for harsh environments.
- High Torque Density: SRMs can provide high torque density, making them suitable for applications requiring high torque in a compact size.
- High Reliability: The absence of brushes and permanent magnets contributes to high reliability and reduced maintenance.
- Potential for High Efficiency: SRMs can achieve high efficiency in certain applications, especially when optimized through advanced control algorithms.
Disadvantages:
- Complex Control Systems: Achieving precise control of SRMs requires complex control systems, including sensors and advanced algorithms.
- Vibration and Acoustic Noise: SRMs can produce more vibration and acoustic noise compared to some other motor types.
- Historically Limited Adoption: Historically, SRMs had limited adoption due to control system complexities, but advancements in control technology have expanded their applications.
Applications:
- SRMs are used in various applications, including industrial machinery, robotics, and electric vehicles.
- They are suitable for applications where a robust and simple design, high torque density, and reduced maintenance are crucial.
- SRMs have been explored in electric propulsion systems for certain types of vehicles.
In recent years, advancements in control systems and materials have increased the appeal of SRMs in certain niche applications where their unique characteristics provide advantages. However, they may not be as widely adopted as some other types of electric motors in mainstream applications.
Conclusion
The choice of electric motor depends on factors such as efficiency, power density, cost, and the specific requirements of the vehicle. In many cases, manufacturers choose motors based on a balance of these factors to optimize the overall performance of the electric vehicle. Additionally, advancements in motor and control technology are ongoing, and new types of motors may emerge as the EV industry continues to evolve.